Discussion regarding the art and science of creating holes of low entropy, shifting them around,
and then filling them back up to operate some widget.
27 October 2005
Woohoo!
I am currently enjoying copious quantities of Hoegaarden beer so don't expect any intelligent commentary for tonight.
22 October 2005
A Quick Swipe at "Free" Hydrogen
A company called Alternate Energy Corporation claims to have some process that reacts water with metals to produce hydrogen gas. A quick browse of their website should set off alarm bells for anyone -- the distinct lack of any details on their system for example. Over at theWatt.com we've found some references to systems that burn aluminium to produce hydrogen. Aluminium won't react with water; you must introduce some acid or base to make the process run. Still, let's just imagine that we have the following irreversible reaction with zero enthalpy.
2 Al + 3H2O → Al2O3 + 3 H2
Given that you input 2 moles of Al for 6 moles of H it would require 9 kg of Aluminium to produce 1 kg of hydrogen. But the manufacture of aluminium is extremely energy intensive!!! Running the Aluminum Association's numbers I come up with 147.7 MJ/kg. This means you need 1329.3 MJ to produce one kilogram of hydrogen with an energy content of 142 MJ. This gives me an ERR of about 10 %. Whee.
If I ran a similarly fictitious reaction with iron I would need 18.6 kg of iron to make a kilogram of hydrogen. You can guess where this is going.
Now if we just burned the aluminium with oxygen in air... (we would have rocket fuel)
20 October 2005
Hydrogen Debunked
http://www.efcf.com/reports/E15.pdf
http://www.efcf.com/reports/E16.ppt
I made a PDF version of E16 for those of you without the latest version of Powerpoint.
19 October 2005
A Candle that Burns Half as Bright Burns Twice as Long
The trucking industry is one that has remained practically devoid of technological advances over the past thirty plus years. The fuel economy of transport trucks hasn't improved at all since 1980 (as far back as I have data). This is pretty surprising given that the cost of fuel is currently about twice the pay of the driver when driving at highway speeds. The mean pay for a trucker is $16.00/hr whereas a 5 mpg truck driving at 55 mph burns around $33.00 of diesel. I don't know what exactly to make of the lack of imagination.
I'll use the following assumptions for my hypothetical truck:
Loaded Mass: 35 000 kg
Frontal Area: 12 m2
Length: 15 m
Rolling Resistance Coefficient: 0.007
Rolling Resistance: 2400 N
Drag Coefficient: 0.7
Drag @ 110 km/h: 4500 N
Drag @ 80 km/h: 2400 N
The first and most obvious point of improvement is the aerodynamics. The drag coefficient for semi-tractor/trailers runs about 0.7 which is nowhere near the level obtained by modern automobiles (0.3). There's no real reason for trucks to be worse. In fact the Bladerunner concept shows a great deal of improvement in aerodynamics. They lowered the profile, improved the nose, eliminated the gap between the tractor and trailer, added aerodynamics to the wheels, and smoothed off all right angles.
Drag Coefficient: 0.3
Drag @ 110 km/h: 2000 N
Drag @ 80 km/h: 1000 N
This yields a pretty impressive drop from 6900 N overall resistance at 110 km/h to 4400 N which should result in a 55 % improvement in fuel economy. This can be achieved by cleaning up the aerodynamics of trucks to passenger car levels. I'm not taking into account the lower profile of the Bladerunner which would reduce the frontal area exposed to drag.
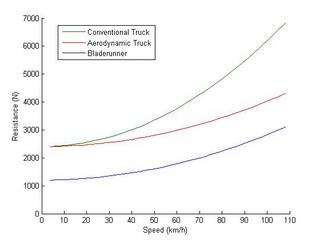
Now to examine the viability of running trucks on rails. The Bladerunner concept has a number of advantages by using the pneumatic tires as the power wheels and the steel bogies for load bearing. It breaks much faster and allows for much higher traffic density on the rail line. However this does come at a price. The rubber tires will no doubt impose their own rolling resistance. The Bladerunner article claims it halves the rolling resistance in exchange for 500 kg of extra mass for the rail bogies. This seems reasonable given that trains are about 3 - 6 times more efficient on the rolling resistance end. This would drop the rolling resistance from 2400 N to 1220 N. Practically speaking the extra mass of the bogies is irrelevant.
So if we compare our aerodynamic conventional truck to our aerodynamic Bladerunner the overall resistance is 4400 N and 3200 N respectively. The improvement in fuel economy is now 37.5 % which may be respectable enough to be economical. The full Bladerunner (3200 N) versus a contemporary (1970-tech) truck (6900 N) represents a fairly vast 115 % improvement. Cutting fuel consumption from truck shipping in half would represent a great reduction in the demand for petroleum.
Practically speaking in order to get the absolute best performance you would want Bladerunners to run in convoys so close together that they would be able to draft off each other. In this case the leading truck would have the hardest drive and the others would cut a break off his slipstream. Since this isn't exactly safe nor fair for the leading vehicle the obvious solution is to actually couple the vehicles in a convoy into a road/rail train. This would require a good communication system amongst the drivers if you wanted to be able to shift trucks in and out of a convoy on the move but it could certainly be worth it. If the vehicles were also hybrids driven by electrical motors then it would also be possible for the trailing vehicles to transfer power to the leading vehicle. In this case the following vehicles could completely retract their rubber wheels from the ground and travel solely on their steel bogies.
The other question to examine is how much is a driver's time worth? We can clearly see from the numbers that from a fuel economy perspective driving 30 km/h slower cuts the drag approximately in half. The disadvantage is that the driver must be paid more to drive more hours and the load will take a little longer to arrive. We can probably discount the amortization of the vehicle itself because that will be based on distance and not time traveled.
At a pay rate of $16.00/hr the marginal cost of slowing down 30 km/h is $6/hr or $0.075/km. With our current bad performance truck fleet slowing down by 30 km/h will shave off about 2100 N resistance, or 2.1 MJ/km. If we have a 30 % tank-to-wheel efficient engine (high side estimate) then we are reducing our burning of diesel by 7.0MJ/km. Diesel has an energy content of 46 MJ/kg and costs about $0.70/kg in the States. Hence our savings for traveling slower works out to $0.107/km. We're saving almost three cents a kilometer by driving slower. These numbers don't work out quite so well for the Bladerunner obviously. The efficiency gains will offset the economics to allow driving at a higher speed.
UPDATE: A quick check of my resistance numbers (6900 N at 30 % engine efficiency) show a burn rate of 23 MJ/km or half a kilogram of fuel. This works out to 4.3 mpg which is less than the fleet average of 5.3 mpg. This would be the case for driving in a straight line without any traffic or stops or hills etc. On the other hand, my truck is heavily loaded. The numbers seem reasonable to me although they could no doubt use some improvement.
Stuart Staniford at the Oil Drum put up a post about the fleet fuel economy numbers. I encourage readers in particular to look at the graph showing fuel economy for trucks. It's flat.
17 October 2005
Basic Bateria Flatulence
There are two basic pathways. The first is the production of hydrogen directly from polymers. The second is a longer process that breaks down polymers to acetate. Methanogenesis can consume either CO2 and H2 or acetate ion (CH3CO2) which also produces CO2 as a byproduct. In addition to hydrogen and acetate some other fermentation products such as methanol can also be transformed into methane.
The acetate pathway is the longer of the two. The first step is the basic fermentation of proteins, fats, and carbohydrates into smaller chunks. The next step is to break down the intermediate products into acetate(CH3COO-) and acetic acid (CH3COOH). The pH of the solution can become unbalanced at this point which is disadvantageous to the consumption of acetane into methane.
The basic reaction is:
C2H4O2 → CH4 + CO2
The hydrogen pathway can consume most forms of biological material. It basic disadvantage is that the enzyme used rapidly reduces in effectiveness in the presence of hydrogen. The very production of hydrogen acts to stall the process. As such the hydrogen must be quickly removed from the system. Diffusion is generally slow but feeding the hydrogen into another chemical reaction can consume it quickly. Because the product is hydrogen gas there has been considerable research into this pathway. Research has focused on genetically modifying the enzyme to operate in the presence of hydrogen or engineering improvements to increase the yield. Methanogens (methane production bacteria) can react H2 with CO2 to form methane. This will produce oxygen gas which is not desirable in the anaerobic environment.
The basic reaction is:
CO2 + 2H2 → CH4 + O2
Methanogensis can only take place in an anaerobic environment. Maintaining an anaerobic environment not only protects the oxygen adverse bacteria but also prevents the growth of oxygen breathing methane burners.
The rate of methane production is highly dependant on pH and temperature. Most methanogens (mesophiles) prefer a temperature between 30 - 40 o and a pH near neutral (7.0) or slightly alkaline. My inability to find temperature and pH dependence is one of my stumbling points at the moment.
Methane producers are not the only bacteria in the pond that consume hydrogen and acetate. In particular, sulfur and nitrogen fixing bacteria both out compete methanogens for reactants. Sulfur fixing bacteria like to produce Hydrogen Sulfide gas (H2S) which then bubbles off and should be separated from the biogas flow. On the other hand, nitrogen fixing bacteria tend to produce ammonium ion (NH4+) which then finds something else to bond to. Ideally one might want to search for a bacterium that fixes sulfur into a solid form that is suitable for soil fertilization. Principally one could find data on the N and S content for Canola meal and figure the number of moles of H2 consumed.
Just as an aside, I did find some research on the production of butanol from biomass instead of ethanol. I don't have on-line access to this research so I can't easily review it but it is interesting nonetheless.
16 October 2005
On The Rails
I thought it would be valuable to look at the major reasons why trains are more efficient than trucks. There are three main areas to look at:
- Air drag
- Rolling resistance
- Transient accelerations
Fd = 1/2 cdρAcv2
where Fd is the drag in Newtons, cd is the coefficient of drag, ρ is the density of air (1.17 kg/m3), Ac is the area cross-section, and v is the velocity in meters per second. For cargo transportation we should normalize the coefficient of drag by the ratio of the cross-sectional area to the overall length of the cargo carrier.
The rolling resistance on the other hand is not very dependant on speed. Drag is usually expressed as
Fr = crgm
where Fr is the rolling resistance in Newtons, cr is the coefficient of rolling resistance, g is the acceleration of gravity (9.81 m/s2) and m is the mass in kilograms.
Transient accelerations basically refers to traffic and hills. Trains have right of way so they don't have to stop and yield to other traffic at any time. Their rail lines also tend to go through or around hills rather than over them. As such they do not waste energy by speeding up or slowing down unnecessarily. Regenerative braking can mitigate this issue to a large extent.
Let's take a look at an example for a car, semi-truck, and a 50-car train.
Transport | Car | Semi | Train |
cd | 0.3 | 0.7 | 2 |
cr | 0.01 | 0.007 | 0.0015 |
L:A ratio | 0.5/m | 3.5/m | 175/m |
Trucks are less aerodynamically efficient than cars for a variety of reasons: their blunt front-end, many exposed turning wheels, gap between the cab and trailer, and the sharp back end. I don't really know how aerodynamically efficient a train is but I can guess that it basically creates its own wind. On rolling resistance trucks have a minor advantage over cars because they operate at higher pneumatic pressure. The steel wheels on trains don't deform at all so they are considerably superior.
The key point is in fact the length to cross section area ratio and its impact on aerodynamic drag. If we normalize the coefficient of drag by the L:A ratio the results for cars and trucks are on the same order of magnitude, 0.6 and 0.2 respectively. The train normalized drag coefficient is dramatically lower at 0.01. Essentially because the front cars will push the wind the remaining cars get a free ride against air resistance. This reduces the overall air resistance on a train per unit mass of cargo regardless of its aerodynamic shape.
If we assume a mass of 35,000 kg for the semi and 2,500,000 kg for the train we can graph an estimate for the rolling and drag resistance:


The resistance at 108 km/h (30 m/s) works out to 0.16 N/kg for a truck and 0.02 N/kg for a train. In this estimate the train is about eight times more efficient. That matches well with generally quoted values. What's more significant is how the rolling resistance forms a much greater proportion of losses for the train compared to the truck. This underscores how the long length of the train gives it an advantage on the drag side of the equation.
11 October 2005
Photoelectrochemical Alternatives
The Energy Blog had a post detailing electrochemical photovoltaic cells that are capable of directly producing Hydrogen gas. It has a pair of advantages:
- It reduces the electron current on the PV cell by consuming the electrons. This should result in a decrease of the recombination of electron-hole pairs.
- The electrolyzer is effectively integrated into the system.
I do not think too highly of this concept. It makes several requirements of photovoltaic systems:
- The active semiconductor material must be capable of resisting corrosion from the hydrogen.
- The semiconductor's band gap must be well matched to the radiation spectrum of the sun.
- The redox potential of water must be well matched to the band edges of the semiconductor.
Simply put, there are no known materials that can meet all three criteria simultaneously. The solution seems to be to produce triple-junction cells to produce mediocre hydrogen conversion efficiencies. I remain unimpressed. Nature simply has not cooperated in providing an appropriate material.
If we take off our hydrogen goggles for a second an alternate solution presents itself. Instead of searching for a suitable semiconductor material perhaps we should search for an appropriate reversible reduction-oxidation reaction. I am thinking specifically of flow battery concepts.
The big name in flow batteries is VRB Power of Vancouver. They build a type of flow battery that uses Vanadium electrolyte to store power. In addition to the Vanadium concept, there are many other redox reactions that have been implemented such as Zinc-Bromine and Sodium Polysulfide Bromine. Such a coupled electrolytic photochemical system would probably still require a membrane to separate the positive and negatively charged electrolytes. Unlike the water reduction, the products won't bubble off as a gas; bromine systems may be an exception.
By introducing another degree of freedom by allowing the redox reaction the number of possible permutations between semiconductor and redox will greatly increase. This increases the likelihood that a natural match will be found to create a solar energy solution coupled to a storage technology.
There's no need for storage coupled to solar energy for on-grid applications yet. On the other hand, off-grid applications do tend to have very large battery packs. The main question is would the extra cost of the flow battery be offset by the superior energy return rate? My gut feeling is no -- off-grid applications are typically very small with electronics designed to minimize power drain.
10 October 2005
Basic Biodiesel Economics
A list of Canola prices can be found here, denominated in Canadian dollars. To summarize since 2000:
Year | Crop Average Canola Oil Price (C$/ton) | Crop Average Canola Meal Price (C$/ton) |
2000 | 568.84 | 156.27 |
2001 | 485.54 | 205.05 |
2002 | 633.10 | 222.80 |
2003 | 813.70 | 214.38 |
2004 | 811.16 | 240.76 |
2005 | 660.22 | 205.40 |
Mean | 662.09 | 207.44 |
Standard Deviation | 131.09 | 28.36 |
For the degummed oil, one metric ton is approximately 1000 L of diesel equivalent or 220 US gallons. Given an exchange rate of about C$0.85/US$, we can find that the basic input price for the oil should be around $C0.66/L or US$2.5/gallon. The cost to process vegetable oil into esters needs to be added to that to determine a final price for biodiesel. Without tax breaks for biodiesel it is not competitive with the fossil fuels. The price of crude will have to approximately double for biodiesel to be competitive.
The story for the meal to methane is slightly different. If we get 500 kg of methane gas from every 1000 kg of meal input, we'll get out about 28 GJ worth of gas. That works out to about US$6/mcf for natural gas which is about half the going rate in North America. If the bioreactor could be built sufficiently cheap this could end up being cost effective now. This is ignoring the inherent value in the remaining sludge as fertilizer.
How about Kyoto carbon credits you ask? Methane will produce about 2.75 tons of CO2 per ton burned. At US$35/ton(CO2) that's about a $50 carbon credit per ton of meal. Alternatively it's US$1.70/mcf. (Not sure why I'm pricing carbon credits in US dollars here...)
For methyl oleate ester you have 38 hydrogens, 19 carbons, and 2 oxygens per ~300 amu molecule. The fuel to CO2 multiplier is about the same as methane at 2.8. On a mass basis biodiesel as 87 % the energy content of fossil diesel. We can apply for a Kyoto credit of about US$85 per ton of Canola we transesterify into biodiesel. This works out to approximately US$0.40/gallon. So the Kyoto credits can make a substantial impact on the cost of biodiesel for those countries that have signed the treaty and are serious about implementing it. It might be useful here to also take a look at costs for other smog and acid rain pollutants which the USA does trade in.
These are some very rough calculations but they show about where the break even points are for biofuels. What's most interesting to me is that because natural (fossil) gas is so expensive biogas may be the most economically viable biofuel in North America at the moment. Surely there are cheaper sources of biomass available than high-protein canola meal. Since the gas situation isn't likely to improve soon investments in this area are plausible. Biodiesel, on the other hand, isn't ready for the big time quite yet.
09 October 2005
Can You Smell the Freedom ExhaustTM?
Generally speaking in we want the oil with the lowest surface tension so that it will flow through the fuel injection system easily and atomize in the combustion chamber well. This means we want to use unsaturated, short chain fatty acid. If we compared oleic acid with its saturated version, stearic acid, we can the difference in viscosity and melting temperature. Also we could compare oleic acid, with 18 carbon atoms, to erucic acid with 22 carbon atoms. Actual distributions of fatty acids in crop types can be seen in this table from Iowa State University. The table shows that Soya has a 8-15 % saturate content, versus 5.6 % for Canola or 11.2 % for traditional rapeseed.
Canola is a cultivar of rapeseed developed in Canada in the 1970s. It specifically bred out eruric acid (long-chain) content and increased the content of 18-chain unsaturated oils. This turns out to be to an advantage for the production of clean burning biodiesel. Canola also bred out glucosinolate content which may lower the pest resistance of the crop. On the other hand, the glucosinolate molecule contains sulfur and nitrogen. Canola has been genetically engineering by firms like Monsato to be herbicide resistant in an effort to increase crop yields. Unfortunately canola cross-pollinates between fields so issues with so called monster food aren't avoided in biodiesel production.
The check variety of Canola (to which other types are compared) is 46A65. It has an average yield of 49 bushels/acre which using this conversion table works out to 2.746 tonnes of biomass per hectare in middle and short growing zones. The longer growing system zones (mostly in Manitoba) can show yields up to 28 % higher. The highest yielding variety from Canola Council trials appears to be a set of Bayer CropScience varieties (5020, 5030, 5070) all running approximately 125 % yields. This is a herbicide resistant crop running the Liberty system. The yield would then be 3.432 tonnes/hectare.
The next step is to examine the composition of Canola. Government statistics show that the oil content is approximately 43 %. There are a variety of ways of extracting the oil from the plant which I will probably discuss at a later date. The remaining biomass (canola seedcake) has a number of potential applications. It can be composted and reapplied to the field but this does not take advantage of the energy stored in the biomass material. It can be sold as high-protein animal feed. It can be burned as biomass to produce heat and electricity as an alternative to coal. It can be fermented into alcohol fuels but the energy return on fermentation is poor. My alternative is to compost the biomass anerobically in water to gather methane from the biomass while retaining the nutrient content that would go up in smoke if the material was burned.
The overall composition of the canola harvest can be estimated by looking at the composition of canola meal and working back from about 40 % oil removal.

As an aside, here's the NREL algae biodiesel study link if anyone was looking for it.
07 October 2005
Integrated Biofuel Co-op
A big part of my shtick is that through a combination of conservation gains and offsetting load to electricity that it would be practical to produce and consume biofuels as our portable fuel of choice. Still I have to say to myself, "do the math stupid." Too many ideas attractive paper concepts don't stand up to rigorous analysis. As such I would like to do a systems analysis for an integrated biofuel farm setup. It would be run as a co-operative by many farmers who grow not just biodiesel but food and other cash crops.
An abstract diagram of the concept is below (click to enlarge):
Integrated Farm Biofuel Layout
For the moment I will use rapeseed (aka Canola) as my oil source, wheat as food, and clover as a nitrogen fixing rotation. Rapeseed appears to be the best crop for biodiesel production in Northern climates (ignoring algae schemes for now). Its yields are significantly below that of tropical palm kernel oil although that does not necessarily mean anything on an energy return basis.
By integrating the production locally I hope to realize higher well-to-tank efficiency for the farm machinery. A local biodiesel plant will reduce the cost of distribution for the farm tractors. Similarly the trucks that transship the farm producst to to a pipeline or train depot could fuel up literally at the well. The transesterification of biodiesel will require either ethanol (derived from seedcake) or methanol (derived from the biogas).
The seedcake and other farm waste goes into a set of solar ponds (not the salt gradient variety). Filled with methane farting bateria they mangent away on pretty much any organic material thrown their way. The biomass is slowly converted to methane gas which is then captured, compressed to a high pressure and stored on-site in tanks. The biogas can fill a number of local uses. It can be burned to provide energy inputs for biodiesel production. It can be used locally for home heating, irrigation pumps, etc. Or it can be shipped off in compressed natural gas tanker trucks. By being a net producer of natural gas the farm co-op should be insulated from variations in the price of fertilizer production. Ammonia and potash production are particularly dependant on natural gas.
Electricity is produced locally as well. Wind turbines are sited when viable, and linked to a local substation that does voltage regulation. A electricity storage system may be located on site to make the electricity production more reliable. A solid oxide fuel cell or steam turbine operates as a combined heat and power plant for the biodiesel production facility.
Writing the entire analysis in one sitting is totally infeasible. I have too much material to explore and learn. I would like to take a blog-style approach to the problem and break it up into its constituents and post them in turn.
04 October 2005
TheWatt Gets a Standing Eight-Count
We hope to have normal news service restored as soon as possible.
03 October 2005
Uber Atomic Battery
While Plutonium-238 can be bred in a nuclear reactor fairly easily, I did start to wonder if there's a better radioisotope out there.
As you can see from the nice diagram I stole from Hyperphysics the natural Thorium-232 chain does contain a nice radioisotope decay chain starting at Radium-228. The overall half-life of the chain is only about 8.6 years and it drops 20 amu over that time.
So how much power does Ra-228 contain? Well I get to go through a radioisotope table and add up the decay energies. It works out to 38.575 MeV along the most popular decay path. If we convert that to moles it works out to an impressive 3.72 TJ/mol, or 16.3 TJ/kg! This is more energy than fissioning Uranium can produce, but less than light element fusion.
The power density is quite impressive too. While the radioisotope starts off slowly with the beta decay of Ra-228 to Ac-228, it quickly picks up speed after a couple years. This is a curious advantage for a space probe: you don't want the RTG to be producing power on the ground because radiating the heat is difficult.
If you approximate the decay as chain as Ra-228 → Th-228 (half-life 6.7 years) and then Th-228 → Pb-208 (half-life 1.9 years) then it's fairly straightforward to find the power output. The power output is in excess of 20 kW/kg from about 1.5 years to 10 years. This is a minor 3300 % improvement over the Plutonium radiothermal generators.
Since the nuclear reactions here are alpha and beta decay, only charged particles are emitted. These are relatively easy to capture in magnetic fields and produce electricity from directly, as opposed to the neutron production in fission reactors. You would of course want to capture the energy emitted with a very high efficiency because radiating it is difficult. Also, the half-life is quite short and the decay ends as relatively harmless lead, so there's not much of a waste problem.
There are some obvious drawbacks. For one, the power output is so massive that a block of Ra-228 wouldn't exist as a solid -- it would produce enough energy to vapourize itself. Thin films could probably exist as solids. It also has Radon-220 in its decay chain -- a very unnice gas. Then there's also the point that it's the ultimate material for a radiological weapon. But these are only minor pettifogging details next to the production question.
While Ra-228 occurs naturally from natural Thorium-232, notice the 14 billion year half-life of Thorium. Given the short half-life of the decay chain, the preponderance of Ra-228 in natural Thorium will be incredibly low. Unless someone has a way of inducing alpha decay I don't know about, this leaves one alternative: transmutation.
Transmutation generally involves smacking protons into a material to make a heavier one. Looking down the periodic table there isn't a suitable atom for Radium transmutation until we get to Bismuth-209. The other elements (Po, At, Rn, Fr) don't occur in any significant natural abundance. A suitable light atom counterpart would be Fluorine-19. Here we have one advantage at least: Bismuth-209 and Fluorine-19 are both the only naturally occurring isotopes of those two elements. As a plus, both are cheap. On the negative side, the result would be Rutherforium-228 which isn't a known isotope and it would quickly fly apart. I.e. we have too many protons, not enough neutrons. Boron-20 simply isn't realistic. A better idea might be to smash deuterium nucleai into Ra-226 (half-life 1600 years), which would produce Ac-228 (the third element of the Thorium decay chain). This would certainly ramp up the power output at the expense of duration.
So the objective is to accelerate a positively charged ion up to some relativistic velocity and smash it into a heavy atom target to make Ra-228. There's two basic particle accelerators: the cyclotron and the synchrotron. The biggest cyclotrons in the world, like TRIUMF, can accelerate protons up to 500 MeV/amu with very high beam densities.
The synchrotron can do better. The Brookhaven Relativistic Heavy Ion Collider (RHIC) runs 100 GeV/amu and proton units at Fermilab and CERN are way bigger. The synchrotron has no real fundamental upper limit other that cost.
Of course, now if we start thinking the following question asks itself: if the ion acceleration energy is less than the 38.6 MeV we get from the decay chain, can we use this Earth-side to produce power? The critical observation is that we are spending kinetic energy to produce nuclear potential energy. The process is simply moving mass from two stable equilibria to an unstable equilibrium. The energy return rate could be enormously high if nature is kind (as if).
None of the processes involved has an inherent low efficiency. Particle accelerators use electromagnetic fields which transfer energy very efficiency. Radioisotope yields can be in excess of 90 %. The decay products are all charged particles, which can be efficiently captured or at least the system can produce high temperatures to drive a heat engine. Also realize that the kinetic energy of the ion is not lost when transmutation occurs. Instead it's converted to heat. That heat can be recovered and used to produce electricity, in effect reducing the power input for the accelerator. Check out this proposal for just that.
Unfortunately I have no idea how to estimate the energy needed for atomic fusion. It's probably significantly higher than 38.6 MeV or someone else would have already suggested the idea, right? As a potential power source for space applications it remains intriguing even if the energy balance is negative. There's also the possiblity that there's superior decay chains that I haven't noticed (Th-229 is good), especially those with higher Z than 240.
Zoom zoom...
02 October 2005
Coal is a Hydrocarbon (Sort Of)
ΔH(C) = -32.7 MJ/kg
ΔH(Coal) = -27.5 MJ/kg, % C = 65% by mass
therefore only 21.255 MJ/kg of energy from coal is derived from burning carbon. The remainder must come from either the combustion of Sulfur or Hydrogen. Sulfur is a fairly trivial component, being 1-2 % by mass and it only provides ΔH = -4.63 MJ/kg.
This means that roughly 27.5 MJ/kg - 21.25 MJ/kg = 6.2 MJ/kg of the heating energy is derived from Hydrogen. The only other potential energy source is Carbon double bonds but I have no way of estimating the frequency of those. Since the H-C bond and H-H bond are quite close in terms of energy I'll just assume that all of this energy is provided by the production of water at 141.9 MJ/kg. That gives a Hydrogen yield of 0.0437 kg(H2/kg(coal). This is surprisingly high -- it suggests my reference coal is almost the equivalent of Benzene. There's only 1.35 C atoms for every H atom. I am mildly suspicious of this result. It is in the right order of magnitude from this table for Australian coal.
This changes the chemical yield of coal gasification slightly. If %C = 0.65 and %H2 = 0.044 then each kilogram of coal yields 0.109 kg(H2) + 0.044 kg(H2) = 0.15276 kg (H2). This represents a 40 % increased chemical yield over my original coal gasification figures! The coal → Hydrogen yield is now 6.54 kg/kg.
Including heating input (7.2 kg/kg), the total coal input drops to 13.75 kg/kg. The fuel cost of Hydrogen derived from gasification drops from $0.72/kg to %0.61/kg. The CO2 production drops to 33 kg(CO2)/kg(H2).
We can run the comparisons to electrolysis at the two price levels once again:
Electricity Price | $40/MWh | $74/MWh |
Gasification Price delta | $1.49/kg | $3.28/kg |
Gasification CO2 Price (33 kg CO2:1 kg H2) | $45/ton | $100/ton |
The average improvement is about 25% over my previous calculations in favour of gasification. Further improvements to the thermal efficiency of the process will only make minor improvements in the cost of coal derived Hydrogen, but it will further depress the CO2 production and make it more difficult for electrolysis to compete.